EPISODE 29
Podcast: John Bolto on 3D Printing in Industrial Supply Chains
John Bolto is a specialist advisor at AdditiveNow, a joint venture between Worley and Aurora Labs.
John is experienced as global technical director for minerals, metals, and chemicals throughout Australia, Europe, and North America, and has managed several technology start-ups before joining AdditiveNow. Their mission is to bring the next generation of manufacturing to the world: additive manufacturing, also known by the more popular term, 3D printing.
On episode 29 of Supply Chain Next, Richard Donaldson talks with John Bolto about the impact on additive manufacturing within the supply chains of the world, the tremendous waste in traditional manufacturing, and how he sees 3D printing changing industry going forward.
You can listen to the podcast below, or watch the video version on YouTube.
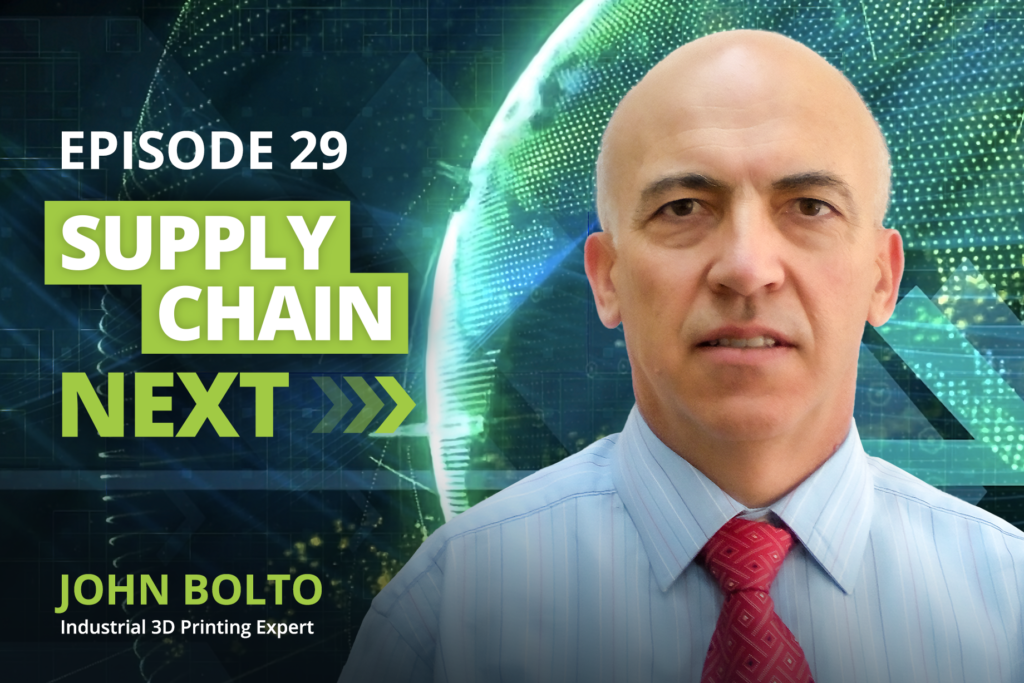
Highlights from the Conversation
Welcome to episode 29 of Supply Chain Next! We’ve got 3D printing expert John Bolto with us here today and this is going to be really interesting. 3D printing is poised to change how we see supply chain in a big way.
In keeping with our tradition here on Supply Chain Next, I want to ask you John: how did you get into 3D printing? Please give us a tour of your journey up to this point.
- It’s really interesting because my background is in mining, oil and gas engineering and project development.
- I was curious about the impact that 3D printing would have on the business I was working in. This is where I discovered additive manufacturing.
- The transition is coming where projects will be virtually designed and virtually manufactured. It all starts out electronically before anything makes it to the real world.
- This is already happening now. Virtual plants are made and run so people can see how everything is working.
- We came to the conclusion that our business knew absolutely nothing about additive manufacturing and we figured it was about time to start learning about it. That’s when we started AdditiveNow. It’s designed to be a part of the additive manufacturing business for mining, oil and gas.
- That’s how we got involved. We’ve had the business running for about 2 years now.
Additive manufacturing, or 3D printing, has been around for a lot longer than that. First, “plastic printers” were created in the 1990s…
I just need to ask you a quick question before you continue.
Can you please clarify the difference between additive manufacturing and 3D printing?
- They are effectively the same thing but we’re trying to give a more well-rounded term to describe the whole suite of technologies. People see plastic printers and think that’s it.
- There is plastic and metal printing but there’s also up to 15 other technologies and each of them have their own niche in the additive manufacturing landscape. Even though all of them are additive in the way that they create things—rather than subtractive—they don’t add them in the same way.
- There’s four or more plastic printing technologies, there’s six or eight metal printing technologies, and then there’s ceramics and glass. And others…
- They even print food these days but I think that’s more of a gimmick than anything else.
As a big science fiction fan this subject has me thinking about Star Trek and the replicators. And they 3D print body parts in another show I’ve seen…
To some people the idea of 3D printing food and other organic material isn’t that far-fetched.
- I was in Singapore before all of the lockdowns started and one of the universities was doing the work for the Mars missions of the future and they were printing dirt. Not something you think about doing.
- They print concrete for home building these days and it’s becoming more common across that industry.
- 3D printers aren’t like the printers we’re used to. They’re 6 meters high and 18 meters wide. They’re big industrial-scale machines but their sizes can vary depending on what they’re designed to handle.
Let’s go back and double-click on AdditiveNow. What is your company up to these days in the world of additive manufacturing?
- AdditiveNow is a service company to the additive manufacturing industry and the resources industry. We aim to be an intersection between those two.
- Our aim is to facilitate the transition of traditional supply chains within complex technological industries to incorporating some aspects of a “virtual supply chain”. This has four different areas. We look at advisory work, design work, printing to qualify a part to ensure consistency, and agile manufacturing.
- We’re not looking to compete with the multinationals who are able to produce thousands or hundreds of thousands of parts.
- There’s a niche in the business to help resource operators to transition from knowing nothing about additive manufacturing to knowing enough to make the parts they need at the right level of quality to build trust in this emerging space.
- Additive manufacturing is already competitive in the short-run manufacturing space.
- The two partners in additive manufacturing are Worley and Aurora Labs. Worley is a large multinational engineering company and Aurora Labs is a small company out of western Australia that makes 3D printers.
- Worley had zero knowledge about additive manufacturing so Aurora Labs stepped in to guide them in this area of technology.
- We’re printer and technology agnostic. We have to be this way because every client’s requirements are different. We must be adaptable.
- We use a number of different print manufacturers from here in Australia, and from around the world, to supply the parts that we deliver. We do a full service so we can advise companies on how to make the transition to additive manufacturing. For example, we can help you redesign your parts so you can get the most out of the process as a whole.
- Then we can produce the parts and get them certified. Many of the industries that we work with have engineering and insurance requirements concerning the certification of the 3D printed parts. They need to make sure that the 3D printed parts are up to the level of quality required by the respective industries and policy makers. This means the parts must be up to code and fully certified.
- One of the reasons we’re talking together today is that there is a need for a digital catalog of 3D printed parts. There’s some crossover between what AdditiveNow does and what Requis does, and this gives us a chance to optimize the platforms to better serve the industries of the world.
Additive manufacturing and supply chain definitely have an evolving future together.
Let’s focus in on 3D printing as a component of additive manufacturing. For example, if I take a look at all of the stuff in my life, all of the things that are scattered around my house, it doesn’t really take as much to produce all of these things as people generally think.
Can 3D printing catch up to this level of manufacturing? If so, what is needed to get there?
- If we take a look at polymers, most of the major polymers are being 3D printed. If it’s something made from thermoplastic, you can 3D print it. Some of the plastics that exist don’t have that property so they can’t be additively manufactured.
- As far as metals go, most of the metal printing technologies are advanced forms of welding technologies. So anything that you can weld, you can print.
- Metal printing has a very high level of control over the entire process and this results in the ability to print things that would be very difficult to weld.
- There are still things you can’t print and most of them are things that have cracking or distortion problems. A classic example would be cast iron.
- Something that is approaching printability is tungsten carbide. There are people who are printing this but it is still at the most early stages of development.
3D printing has a very granular level of control compared to other manufacturing processes.
Can you elaborate on the properties of the base materials that are capable of use in the additive manufacturing process?
- There’s two basic ways of accomplishing this from the base plastic or metal powder.
- One way of doing this is fairly well known. The 3D printer has the base material (powder) heated up to the right temperature and then is dispensed into the required shape via a printer head. The material is then cooled into what you need it to be.
- The other way of doing this is to lay the powder in layers (thickness measured in microns). The layers are stacked together to form the shape you need.
- Plastics can be bound together with glue or heated up with a laser. The same is true for metals.
- The final step is curing: a plastic product needs to be cured, while metal products complete the final step in some type of furnace to finalize the binding of the powder base material.
- There are different levels of density possible during the final steps of the binding process.
- Another process exists where the base material is accelerated into the mold where you want the product to form.
So we’ve got the materials down. What about the printers? Can you tell us about where the 3D printers are in their evolution today?
- The interesting thing is that the printers are still quite large but they are mostly used to print small products.
Where else is additive manufacturing in use today?
- Most industries are using some form of 3D printing today within their supply chain even if it’s only a small part of what they do.
- The medical and dental industries are using 3D printing much more and is quite a significant part of what they do.
- 3D printing is used quite extensively in the aerospace industry to produce lightweight products.
- They are using 3D printing quite extensively in the automotive industry too where it’s a solution for prototyping. It can reduce the prototyping innovation cycle from three to six months down to a week or two. The best example of this is Formula One (F1) racing where they can go from idea to printed part in seven days.
That innovation cycle is incredible…
- It is. The most pervasive use in F1 is the aerofoils and the shape of the car where they can test aerodynamics quickly.
- In F1 very small changes to a part can have a big impact on the performance of the car. F1 is at the leading edge of aerodynamics and 3D printing is helping their research and development.
- Parts in the F1 engines are made from lightweight material and those are very printable. They also try to aggregate parts of the engine to make the cars more lightweight and more easily maintained.
- Additive manufacturing has the ability to remove metal from a part without changing the part’s strength due to the design process where an extreme level of granular control is possible. This is used in F1 to make their cars lighter and faster.
Let’s examine how this is affecting space research considering the successful landing on the comet. New minerals were discovered there. Perhaps those minerals could have enhanced 3D printable properties as a base material?
- They are considering using 3D printing in space, which is a good place to do printing due to the lowered oxygen. But the lowered gravity presents a challenge.
- Mars would be better to do 3D printing than a zero gravity site such as the International Space Station or spacecraft. Gravity is used in the printing process.
I’m glad you brought that up. I didn’t think about the use of gravity in 3D printing.
So we’ve got 3D printing across many industries. Where do you see 3D printing breaking into other industries?
- In the energy, chemicals, and mining industries it is in an early adopter phase.
- The medical industry is using it at an increasing rate but there are some standardization issues present there.
Aerospace is getting there but it’s still being examined. - The military has accepted additive manufacturing as a potential solution coming in the near future, especially for manufacturing in the field.
- In the oil and gas industry, or the chemicals industry, it’s being considered to reduce the capital held in their spare parts. Instead of storing spare parts that aren’t needed they are considering print-on-demand solutions. This can save money in many areas, mainly storage and shipping.
- If people can print what they need on demand instead of storing spare parts they can improve their bottom line.
Many are doing research to discover what parts can be printed by testing various use cases. For example, 3D printing can be used to create a custom part to replace something that has corroded to the point where a different form of manufacturing would be too complex and expensive (to create a customized part). This introduces the ability to create solutions that were previously inaccessible. - Take a hydraulic hitter for example. They make those from solid metal and each part is machined separately and then aggregated into one product with seals between each of the parts. The least reliable parts are the seals between the metal parts.
- When you additively manufacture a product like this you can make it without the seals between the parts. It’s made as one part.
- They are being used in the field to test their reliability and are made from stainless steel, which is very printable.
Additive manufacturing is positioned to really change supply chain. Where do you see this going?
- With print-on-demand, the need to store parts on a shelf will be reduced, which changes the design and behavior of the supply chain.
- A business would only have to pay to print the part. If you can manufacture a part right where it’s needed you remove many steps from the supply chain, which will naturally optimize operations and reduce costs by removing several steps from the supply chain, such as shipping. Carbon is removed or reduced from the footprint of that part as well.
- Think about a large sophisticated valve that is produced for the oil and gas industry. It could go around the world three times before it actually finishes up with the client because each piece of it is produced in different countries. Then it’s assembled in yet another different country which of course isn’t near where it’s actually needed, so it must be transported again.
- The future is the localization of the production and drastically simplifying supply chains.
- A lot of the specialist knowledge required to produce a product is embedded into the design. Once you have access to the design and the right base material powders you should be able to manufacture the part you need right where you need it.
- All post processing, such as heat treatment, is embedded into the additive manufacturing of the part.
- The design information is stored in an encrypted bundle which must be decrypted before it is given to the 3D printer. In the future the printers will have the decryption ability built into them.
- So it’s literally “on demand manufacturing”.
This would massively reduce the amount of resources required for manufacturing, processing, and shipping.
Can you talk a little bit about the circularity within all of this? Can we turn the printed part back into the base powder to be used again?
- Let’s compare the waste produced with reductive manufacturing versus additive manufacturing.
- You put the base material powder into the printer and fuse it to make the part. The powder that didn’t make it into the final product is reusable.
- Copper is a great example here. The original copper that was mined many years ago is still recycled constantly and used over and over again. Copper has very high recyclability.
- The recycle rate of aluminum and many types of steel are improving too.
- There are non-trivial advantages to the powder base material used in additive manufacturing compared to traditional manufacturing. The main one is that the powder used in additive manufacturing is in a form where it can take any shape required. This massively cuts down on energy waste by removing the need to reform bulk metals.
- This cuts down on the storage and processing of big blocks of metal.
- With the base material for 3D printers you just mine the metal, process it into the powder form, and then it’s ready to take any shape required.
So what do you see coming up in the near future for additive manufacturing?
- Our clients are starting to see the advantages of additive manufacturing and are beginning to integrate this into their future plans as a way to cut costs and improve their supply chain operations.
- 3D printing reduces the carbon and waste footprint of all companies who use it. Big oil companies like Shell are beginning to put pressure on their OEM suppliers to integrate additive manufacturing into their daily operations as soon as possible.
- When manufacturers put their clients first everybody wins.
- Additive manufacturing can optimize supply chains, reduce waste, and reduce operating costs significantly.
Connect with John Bolto
John is ready to connect on LinkedIn.
More Episodes
You can listen to our audio tracks and read highlights for each episode below.
We’ve also started publishing video episodes on our YouTube channel.
058 – Dr Marcell Vollmer – Tech in Supply Chain, and the Sustainability Shift
Supply Chain Next · 058 – Dr Marcell Vollmer – Tech in Supply Chain, and the Sustainability Shift Meet Dr. Marcell Vollmer Dr. Marcell Vollmer, a renowned expert in the fields of digitalization, innovation, and sustainability. Marcell is a sought-after speaker and author that has dedicated his career to helping companies and individuals navigate the rapidly…
059 – Juli Lassow – Revolutionizing Retail, Sustainable Strategies, & the Future of Partnerships
Supply Chain Next · 059 – Juli Lassow – Revolutionizing Retail, Sustainable Strategies, & the Future of Partnerships Juli Lassow ,founder of JHL Solutions Meet Juli Lassow Juli Lassow, an accomplished retail professional, speaker, writer, and sustainability advocate, is the founder of JHL Solutions, a consultancy focused on creating outstanding private-label partnerships. With a deep…
060 – Martijn Lopes Cardozo – Circular Supply Chain
Supply Chain Next · 060 – Martijn Lopes Cardozo – Circular Supply Chain Martijn Lopes Cardozo, CEO at Circle Economy Meet Martijn Lopes Cardozo Martijn, a seasoned entrepreneur, has an impressive track record of establishing prosperous ventures within the realms of software, mobile, and digital media in California. Upon returning to the Netherlands, he…